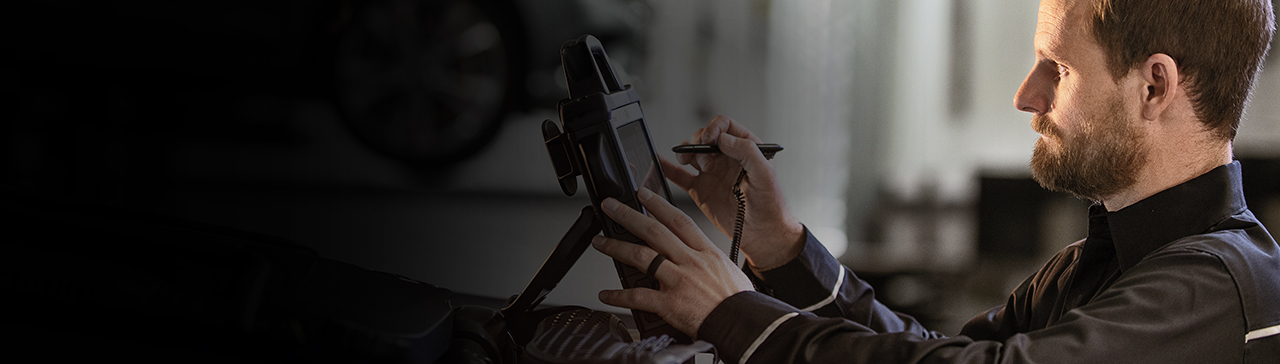
Technical Information.
WIS/StarTek Info Access
-
StarTek Info
StarTek Info is an official Mercedes-Benz USA, LLC site for hosting service and repair technical documentation for Mercedes-Benz vehicles.
-
Workshop Information System
Refer to Mercedes-Benz Workshop Information System (WIS) for detailed repair information on Mercedes-Benz vehicles.
Technical Assistance
Mercedes-Benz USA, LLC utilizes an online technical assistance system named PTSS (Product Technical Support System). PTSS is supported by our DTS (Dealer Technical Support) team. The system allows for internal case escalation where necessary to assist in repairs and populates a knowledge database, which helps other dealers solve technical issues through a system named TIPS.
Vehicle Materials
-
Mild steel, 300 N/mm tensile strength
General Information:
Generally these steels are low-carbon steels which are produced in several qualities for automotive applications. The low carbon content found in these mild steels will perform well with typical automotive welding techniques, but the relatively low yield strength, as compared to other steels, limits its usefulness. Because of its versatility and low cost, low-carbon steel is an effective material for most automotive applications.
Material handling:
Mercedes-Benz standard priorities for fastening techniques apply:
- Resistance spot welding
- Riveting, gluing
- MAG welding
For the repair of hybrid construction vehicles, see the other sections too, especially in case of aluminum and magnesium parts close to the work area.
-
High-strength steel, 300-550 N/mm tensile strength
General Information:
High-strength steels are low-alloyed and offer a justifiable compromise from formability and strength.
Successfully forming a complex part can be difficult, but is possible with a well thought-out design and modern presses. This grade will provide mass reduction in most automotive applications.
High-strength steels are used in the areas of endurance stress.Material handling:
Applicable fastening techniques:
- Resistance spot welding
- Riveting, gluing
MAG-welding permissible
For the repair of hybrid construction vehicles, see the other sections too, especially in case of aluminum and magnesium parts close to the work area.
-
Modern high-strength steel, 550-1000 N/mm tensile strength
General Information:
Modern high-strength steels combine high mechanical strength with a good formability. Due to their good formability and their high capacity to absorb crash energy they are used for areas of high loads in case of an accident.
Material handling:
Applicable fastening techniques:
- Resistance spot welding
- Riveting, gluing
MIG soldering is only permissible on repair points described in WIS.
For the repair of hybrid construction vehicles, see the other sections too, especially in case of aluminum and magnesium parts close to the work area.
Equipment required:
- For cutting, riveting, milling and drilling, special equipment for high-strength steel is required.
- Approved spot welder for high-strength steel is required.
- In case of riveting use high-strength rivets approved by DC only.
- Pay attention to different solder materials.
-
Ultra high-strength steel, hot worked, 1000-1500 N/mm tensile strength
General Information:
In the automotive industries, ultra high-strength steels are an innovation in mechanical engineering, they have been used since 1912.
The substantial advantage of these modern steels is the separation from forming characteristics and using properties. The "hot working" results in a better formability, the final strength is achieved through a heat treatment during or after forming. Their high tensile strength results in enormous weight reduction.
Material handling:
For straightening/repairing, ultra high-strength steels do not heat above 300 C, the maximum permissible temperature for heating the flange connection to be loosened is 200 C.
Applicable fastening techniques:
- Resistance spot welding
- Riveting, gluing
MIG soldering is only permissible on repair points described in WIS.
For the repair of hybrid construction vehicles, see the other sections too, especially in case of aluminum and magnesium parts close to the work area.
Equipment required:
- For cutting, riveting, milling and drilling, special equipment for high-strength steel is required.
- Approved spot welder for high-strength steel is required.
- In case of riveting use high-strength rivets approved by DC only.
- Pay attention to different solder materials.
-
Aluminum
General Information:
Aluminum has already established itself in the car industry. Its low density, the high specific energy absorption performance, the good specific strength, the corrosion resistance and the recycling capability are the most important properties. Aluminum is mainly used for doors and closures but also for structural body parts.
Material handling:
Applicable fastening techniques:
- Resistance spot welding
- Riveting, gluing
Standard aluminum work station:
The basic requirements of an aluminum working area concern the protection against corrosion and explosion. The requirements of an aluminum working area are in accordance with the directives.
It is absolutely necessary to separate the areas for working with steel and working with aluminum:
- as steel shavings and grinding dust may cause corrosion
- as aluminum dust is explosive
The working area must be protected against steel/grinding dust from bodyshops nearby (i.e., through curtains, mobile protection walls or solid partition walls) as done with a fully equipped working area.
Washable walls and floors are necessary for wet cleaning to remove any aluminum dust (no dust extraction with pneumatic tools —danger of explosion!). The working area should have only a few horizontal surfaces, tubes or leads to avoid dust deposits and to enable cleaning with dust extraction or sweeping (no extraction with pneumatic tools &—; danger of explosion!).
All electrical installations and units located in an area where aluminum dust concentration occurs, have to be protected according to the directives (e.g., illumination, sockets, lifting platforms, vacuum cleaners and all other electrical units used in the area. — danger of explosion!).
Existing straightening benches and kits can be used for either application only after having been cleaned carefully.
Further requirements:
- The vehicle to be repaired must be covered completely, except for the area to be repaired in order to avoid consequential damage.
- Whenever grinding on steel is required, i.e., on steel rivets, all aluminum parts must be protected from sparks (danger of corrosion). Important!
- Important!
Separate set of tools intended only for aluminum repair (aluminum workshop cart). None of the tools should ever be used for working on steel parts. All tools for working on aluminum must be marked with a specific color for differentiation.
-
Magnesium
General Information:
Due to its small specific weight, magnesium has become increasingly popular in the premium car segment. It is used in the manufacture of transmission housings or parts of doors for lightweight constructed cars. Pressure die casting permits the manufacturer to create parts with complex geometries.
Material handling:
- If magnesium is ignited, it burns at approx. >500 °C with dazzling white light and severe heat build-up (approx. 2400 C).
- Magnesium dust is just as combustible and explosive as aluminum dust.
Machining/treating magnesium:
- Machining/treating magnesium components by means of an open flame (welding, cutting, soldering, heating, etc.) or by spark-creating grinding/drilling is prohibited.
- Any components that suffer structural damage must be replaced completely.
-
Plastics
General Information:
Plastics are already an important material for the automotive industry. They have a low density, are mostly economic to produce and their characteristics can be fitted to specific demands. The wide variety of properties can be created through chemical or physical material combinations. Plastics can be used to make bumper coverings or exterior attachments to the body structures. Due to their weak mechanical characteristics, plastics will not frequently be used for large-scale structural components such as vehicle floors.
Material handling:
- Structural damaged components have to be replaced.
- Smaller damages can be repaired through Mercedes-Benz "Small Repair" program.